An integrated approach to alternative fuel use in cement making
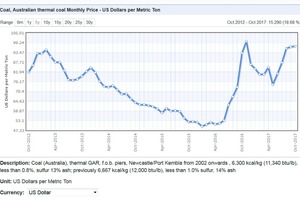
With the world facing new challenges in handling growing volumes of post-consumer waste, linking waste- and raw materials-preparation systems offers a viable solution – and big economic benefits.
1 Introduction
The world is facing a growing challenge with handling the ever-increasing tonnages of waste materials being produced, while at the same time environmental pressures are driving the push to reduce fossil fuel use in industrial processes. Cement production is no exception in this respect.
And while the traditional approach was to regard waste as unwanted, fit only for burying and leaving for future generations to attend to, there is now a much greater appreciation of the value of waste as an energy source in its own right. In every sense, this is a win-win situation, with less physical material to be stockpiled and greater substitution for fossil fuels helping to cut cement production energy costs and CO2 emissions at the same time.
Building on its 111-year history in designing and supplying specialist mills for grinding coal, cement raw materials and clinker, Loesche GmbH has brought together the technologies needed to optimise the production and firing of waste fuel in calciners and kilns. With the group including two companies that specialise in waste milling, pyrotechnology and process optimisation, Loesche can now offer a completely integrated package that incorporates all aspects of waste-derived fuel utilisation in cement production.
2 The challenge of waste
Throughout the world, waste generation is on the increase. This is obviously a result of population growth in general, but other factors come into play as well – such as increasing urbanisation within the developing world. Using data from the World Bank, Figure 1 illustrates the variation in growth rates on a regional basis for the period from 2005 to 2025. During these 20 years, urban waste generation in Southern Asia will have nearly doubled; Africa and the Eastern Asia-Pacific region will not be far behind. And while the World Bank predicts urban waste growth in the OECD countries to be only around 10 %, it has to be remembered that this economic group actually produces 44 % of the world’s total.
There is also considerable diversity in terms of the composition of the urban waste being produced. As Figure 2 shows, in China organic matter makes up nearly 60 % of the total amount; paper, cardboard and plastics – key fuel components of the waste – less than 20 %. By contrast, less than 30 % of the urban waste generated in the USA is organic, while these potential fuel constituents comprise over 40 %.
The traditional approach has been to collect waste, process (condition) it and dispose of it. The conditioning step can, in the right conditions, lead to a proportion of the waste stream being re-used. The challenge here is to improve the quality of the usable material so that more can be done with a greater proportion of the total, resulting in less being sent to landfill or other disposal.
Turning waste into energy is one clear option, but the efficiency of the conversion depends to a great extent on the technological approach used. Figure 3 illustrates the differences in conversion efficiency when using alternative fuels – such as municipal and industrial waste – for energy generation. Data from the German Association for Secondary Raw Materials and Waste Management show that burning this type of waste in a conventional incinerator achieves around 35 % energy conversion efficiency. By contrast, using waste material to fire cement production nearly doubles the efficiency; more energy is won and, of course, the specific emissions from production are reduced.
This fact has not been lost on cement producers, particularly those in countries where the infrastructure is in place to handle, separate and prepare waste materials for use as fuels. Thus, for example, alternative fuels account for over 60 % of the process energy input in Germany’s cement production. In Austria, the proportion is even higher, at over 70 %, with selected industrial and commercial waste comprising by far the largest component within the alternative fuel mix.
3 What’s the cost?
Not only is using waste as an alternative fuel in cement production more energy-efficient, but it is also mostly cheaper to implement. In order to compare the costs and revenues of a recent waste-to-energy project in Latin America with waste utilization as fuel in cement plants, a standard plant with an approximate clinker production of 4000 t/d was considered. The necessary amount of waste to achieve 90 % total substitution rate and the incurring costs as well as primary fuel savings (coal-based) were calculated. In a second step, the waste-to-fuel alternative was scaled-up to equal the amount of waste utilized in the new waste-to-energy plant. Naturally, such a comparison does not claim to represent all possible configurations of either waste-to-energy plants or AF utilization in cement plants, however the results are quite exciting! The total capex for utilization in cement plants would only amount to 30 - 40 %, whereas the revenue (electricity sales versus coal savings) would be in the range of 75 - 85 % when compared to a waste-to-energy plant!
Hence it is clear that both constructing new, and adapting existing cement plants to burn alternative waste-derived fuels can offer significant economic benefits for both capital and operating costs. So what is actually involved in achieving higher levels of fuel substitution, and what are the implications in terms of the technology needed?
For thermal substitution rates (TSR) of 9 % or less on an existing cement plant, little is required apart from work on the fuel conditioning unit, which may need to be installed as new, or expanded in capacity where alternative fuels are already being used. Thus the capex commitment is likely to be limited. Once the initial reluctance of working with waste is overcome, the direction is clear.
To increase the TSR to the next threshold at up to 25 % of the fuel energy input, not only must the fuel-conditioning plant be upgraded, but more milling capacity will also be needed. Where the commitment to alternative fuel use really requires the highest investment comes with the next milestone, taking the TSR from 25 % to 60 %.
In this case, major modifications are usually needed to the plant infrastructure, with modifications to the calciner section and the installation of a chlorine bypass system. Further upgrading to the fuel conditioning and milling capacities will also have to be undertaken.
After that, reaching higher TSR levels builds on the investment already incurred, through measures that are essentially complementary to those already put in place. Higher-capacity fuel preparation systems are again needed, as well as modifications to the main kiln burners to allow them to efficiently handle higher proportions of alternative fuels.
This analysis clearly shows that profitability increases with increasing TSR – and the most significant savings are achieved with the highest alternative fuel inputs, as Figure 5 shows.
4 Understanding the requirements
By bringing together the expertise of its group member companies in the fields of grinding, pyroprocess technology, plant optimisation, energy systems and cement plant equipment design and operation, Loesche is in a unique position when it comes to helping cement producers gain the benefits of using greater amounts of waste-derived fuels. This expertise was widened in 2012 when both aixergee, which specialises in cement plant optimisation and CFD simulations, and the Austrian company A TEC (including Greco Combustion Systems from Brazil) became part of the Loesche group. So now, not only can Loesche supply equipment, but it can also design and undertake all of the modifications that may be needed in order to increase alternative fuel use in cement plants.
Looking at some of these capabilities in more detail, A TEC’s expertise lies in the cement kiln pyroprocess. Since the mid-1990s, the company has been focusing on the use of alternative fuels in cement production, and can now supply complete alternative fuel systems for nearly any kind of solid and liquid waste materials, including materials handling, preparation, storage and feeding into the kiln. In parallel, it undertakes any modifications that may be needed to the pyroprocess for firing alternative fuels, such as to preheaters, calciners and ancillary equipment.
Another of A TEC’s strengths is illustrated by its Rocket Mill technology, designed to produce high-quality waste-derived fuels with special characteristics that allow very high substitution rates. A key benefit is that Rocket Mills can be integrated within a cement plant, allowing producers to manage their own fuel supplies efficiently and with confidence about the output quality, without having to rely on outside suppliers who may not be able to meet the stringent quality parameters needed to achieve high TSRs.
The technology within the Rocket Mill enables pre-sorted, shredded household and commercial waste with a bulk density of 100 – 300 kg/m³ to be ground to a size of 15 mm, with 50 % < 5 mm, in one pass. The preparation process not only provides size reduction but also increases the specific surface area of the waste material, giving better ignition and combustion properties – key factors when striving to achieve high TSRs.
Of particular importance where the raw waste has a high moisture content, the physical process within the Rocket Mill provides a drying effect, such that feed at 25 % moisture can be transformed into fuel containing 15 % moisture or less.
Of course, investment in equipment is just one aspect of achieving a successful transition to using larger amounts of alternative fuels in a cement plant. Bringing expertise in process optimisation to the Loesche group, aixergee can evaluate how a plant functions, identify any limitations and seek their root causes. Having done so, it can then provide appropriate solutions in order to optimise the plant’s operation.
Plant optimisation is not, however, just confined to the situation where a cement producer wants to alter the composition of its fuel mix. Indeed, cost pressures and changing feed and product parameters mean that optimisation is often a continuing requirement, with equipment operation modifications needed on a regular basis. The challenge is that the process inside a calciner or a kiln is different from what it looks like from the outside: hence the need for process modelling of parameters such as the gas- and meal flows, the combustion process, emissions and the clinker quality before actual system modifications are put into effect.
In the case of increased use of waste-derived fuels, aixergee can use CFD and other techniques to model the kiln or calciner behaviour of different waste particles, offering a better understanding of how they flow, interact and burn. The output from these studies can then be used to develop optimisation process flowsheets.
5 Alternative fuel use in cement production
As a general rule, increasing the proportion of alternative fuels – such as those derived from post-consumer and commercial waste – will be an attractive approach for cement producers keen to cut their energy costs. Nonetheless, at the same time it is important to ensure that the plants remains stable in operation, despite potential variations in the fuel composition, and that the quality of the clinker product continues to meet specification. In addition, any system in which large amounts of alternative fuel is burnt must retain low maintenance requirements, since increased service costs would obviously eat into the energy cost savings achieved.
In view of this, it is essential that high-quality waste-derived fuel is used in any system that increases the TSR in cement plants. And this is where the A TEC Rocket Mill brings significant advantages, not only in terms of the way in which it dries and prepares the waste material, but also through its ability to segregate and discharge inorganic matter that has the potential for forming increased amounts of ash during combustion, while at the same time increasing the calorific value of the waste-derived fuel.
Using a high-quality fuel obviously has a positive impact on the pyroprocess as a whole, with better fuel burn-out in the kiln resulting from the improved physical fuel properties. In addition, practical experience has proved that the use of well-prepared, high-quality fuel leads to the production of high-quality clinker, with less iron-rich brown clinker and reduced sulphur circulation. Finally, plant operation remains stable because the fuel is more homogeneous in terms of its chemical and physical properties.
While the Rocket Mill process reduces the moisture content of the waste, even drier fuel can be produced by adding a drier-separator unit to the fuel-preparation circuit, or by flushing waste gas through the Rocket Mill. Fuel produced in this way assists in achieving fast burn-out and helps to maximise the TSR.
Thus TSRs of over 90 % are now being achieved using A TEC’s combustion and post-combustion chamber designs in calciners, with the post-combustion chamber in particular ensuring that full burn-out is achieved even when using high feed rates of alternative fuels. Importantly, kiln stability is also maintained.
6 Loesche’s approach to alternative fuel use
The world has a waste problem. Data from the Waste Atlas show that some 1900 Mt/y of Municipal Solid Waste (MSW) are being produced world-wide, of which only 70 % is collected. Of this 70 %, 19 % is recycled or recovered and 11 % – less than 150 Mt/y – is used as fuel in energy-recovery facilities. Clearly there is an opportunity to divert a much greater proportion of the waste that is now landfilled to energy production with, as has been noted above, the cement industry providing a cost-effective alternative to the traditional type of power station for waste combustion.
Returning to Figure 3, it is important to understand that the efficiency comparison shown here – favouring the use of waste as a fuel in cement production – is based only on the chemical energy contained in the fuel. The study from which the illustration has been derived also concluded that the use of high-quality conditioned waste in cement plants has environmental benefits as well, in that any ash produced during combustion is incorporated into the clinker, so requires no further handling or long-term disposal.
The integrated approach that Loesche can offer the world’s cement producers brings together the company’s strengths in all of the areas needed to make the increased use of waste-derived fuels a success, both technically and economically. The rationale for doing this is strong: Loesche operates within very energy-intensive industries, which are now under pressure to decrease operating costs. Properly selected waste contains usable energy, most of which is currently “going to waste”, so exploiting this resource helps to improve the sustainability of cement production.
Today, more and more countries are taking action to establish sustainable waste management systems. Political and environmental pressures to find a solution are increasing, as more attention is given to public health and safety issues, and to the question of land allocation for waste disposal, particularly around large urban centres.
In addition, primary energy prices have risen by around 80 % in the last years, providing cement producers with a major incentive to start or to significantly increase their total substitution rates.
Loesche’s focus on waste as a valuable resource brings together the company’s expertise in equipment, process optimisation and – most importantly – its long-term understanding of the cement and power industries’ operational requirements. This experience allows the company to provide the best possible solutions for its customers, and by knowing what the end-user needs, it can do this with waste conditioning plants as well as for their grinding needs.
Perhaps the biggest challenge is that waste is one of the most heterogeneous streams available in the world – there is no typical composition. By understanding this, Loesche believes that its integrated approach to providing appropriate solutions to individual cement plants’ requirements offers a clear way forward.
7 Keynote
As can be seen in Figure 7, the tendency towards increasing coal prices is quite clear, so now is the time to invest in higher substitution rates and profit from the significant savings in primary energy costs!
//www.loesche.com" target="_blank" >www.loesche.com:www.loesche.com